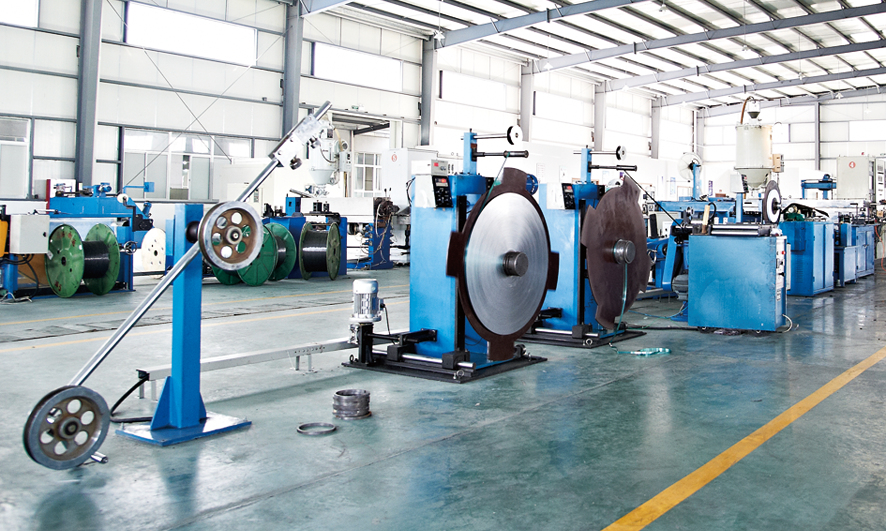
In order to protect the fiber optic cable core from external mechanical, thermochemical, moisture and biological gnawing, the outer core of the optical cable must be jacketed, or even protected by an external sheath. only in this way can we more effectively protect the normal operation and service life requirements of the fiber optic. The production process of optical cable integrated sheath must be able to ensure the production of qualified sheath in accordance with the following requirements:
(1) Completely Sealed. For optical cable, it is very important to prevent the invasion of moisture or moisture that may affect the performance of optical cable and eventually lead to the failure of optical cable. Therefore, the production of jackets must be completely free of bubbles, pinholes and welds.
(2) There are accurate size, good concentricity, smooth surface, especially the inner surface of the jacket.
(3) In order to reduce the connection point of optical cable, the production mode of long continuous length of optical cable should be realized as far as possible. At present, the typical connection length of optical cable is 5km, which can reach 6~7Km or even longer if there are special requirements.
(4) The cable core shall not be damaged in the process of production.
1 Water Blocking Technology of Optical Cable. With the continuous development of fiber optic core and fiber optic cable manufacturing technology and materials, the water resistance technology of optical cable has developed from the earliest gas pressurization water resistance to the current stage of filling water resistance Gel and water absorption expansion materials, and the level of water resistance technology has been greatly improved and developed.
(1) Filling of Gel. Fiber filling gel, cable filling gel or sheath Gel filling is usually filled with special Gel filling equipment: Gel filling machine.We take cable gel filling as an example to briefly discusses. The basic filling principle is to use a high-pressure oil pump to pump the Gel into a specific container, which adopts a reflux device, and an Gel mold with a size matching the cable core is installed at the outlet of the container for two purposes: one is to ensure the surface of the cable core is round; the other is to control the amount of Gel. When the Gel is insufficient or uneven, it will lead to the uneven outer surface of the optical cable sheath. In addition, too much Gel will produce bubbles and necks during the extrusion of the sheath. In the production process, it is necessary to ensure that the Gel is filled evenly, filled and does not leak.
(2) Dry Water Blocking Process. In order to ensure the longitudinal water resistance of optical cable, in addition to gel filling, there is also a dry water resistance process. The dry water resistance process can be divided into two structures: "full dry" and "semi-dry".
2 Longitudinal Jacketing Process. The quality of the longitudinal Jacketing technology directly affects the surface quality and mechanical properties of the optical cable, so the quality of the longitudinal Jacketing is the primary problem of the sheath technology. The longitudinal Jacketing process includes water barrier longitudinal Jacketing, steel (aluminum) plastic composite belt rolling, Core-rod forming, lapping and shaping. In order to ensure that there is no water seepage in the gap between the cable core and the wrinkled steel (aluminum) plastic composite belt, the longitudinal Jacketing process of the water barrier is adopted. The thickness of the water barrier is generally 0.25mm and the width is designed according to the outer diameter of the cable core to ensure that there is an overlap area of 3~5mm after the completion of the longitudinal Jacketing of the cable core. The longitudinal rolling device of steel strip / aluminum strip is composed of a rolling machine and a longitudinal Jacketing machine.
3 Plastic Extrusion Process. The quality of the plastic sheath of optical cable is related to many factors, such as the quality of the plastic material itself, the performance of the extruder, the extrusion temperature, the tension, the traction speed, the cooling mode of the plastic after extrusion, the die design of the machine head and so on.
(1) Plastic Extrusion mould. The die used in the production of optical cable sheath extrusion, including die core and die sleeve, is mainly in three forms: extrusion type, extrusion tube type and semi-extrusion tube type. The structure of the three kinds of mould is basically the same, and the only difference lies in whether there is a tubular bearing diameter part at the front end of the die core or the relative position between the tubular bearing diameter part and the die sleeve is different.
(2) Extrusion die. There is no tubular bearing diameter part of the extruded die core, and the die core is shrunk behind the die sleeve diameter. The molten plastic is finally shaped by pressure through the mold sleeve, and the structure of the extruded plastic layer is compact and the appearance is smooth. The angle between the die core and the die sleeve determines the material flow pressure, which affects the quality of the plastic layer and the extruded optical cable. The disadvantage is that the glue discharge speed is slow, the eccentricity adjustment is difficult, and the thickness is not easy to control.
(3) Extruded Tube Die. Extruded tube type is also called sleeve type die. The die core has a tubular bearing diameter part, and the extrusion method in which the die core end protrudes the die sleeve end face or is flat with the die sleeve end face is called extruding tube type. In pipe extrusion, due to the existence of the tubular diameter part of the die core, the plastic is not directly pressed on the cable core, but moves forward along the tubular diameter part, forming a tube at first, and then stretching and then Jacketing on the optical cable core.
(4) Semi-Extruded Tube Die. The semi-extruded tube die core has 5mm left and right tubular bearing part, which is between the extruding type and the drawing type, and the die core mouth end is basically in the middle of the flatness (bearing diameter) of the die sleeve. In semi-extruded tube extrusion, because the die core is shrunk behind the die sleeve diameter, the molten plastic is shaped by a certain pressure through the die sleeve, and this pressure is much smaller than that of the extrusion type; because in the die sleeve diameter, there is a section of die core tubular bearing diameter length, so it retains some characteristics of the drawing tube die. The molten plastic is pulled out along the tube and then coated on the cable core. The semi-extruded tube die combines the characteristics of extrusion type and extrusion type, and the performance is between the two. It is widely adopted in the sheath technology of ADSS optical cable and some special products.
4 Armored Technology. The armour technology of optical cable is a kind of protective operation process adopted in order to increase the tensile and compressive strength of optical cable and install metal structure layer. The armor layer is located between the inner and outer sheath of the optical cable. There are generally two kinds of armoring materials and methods: steel wire armoring and steel tape armoring. There are two kinds of armoring technology: longitudinal Jacketing process and winding process. There are mainly two kinds of optical cable armour equipment: steel wire armour machine and steel strip armour machine.
(1) Steel Wire Armoring. Generally speaking, steel wire armoring is not needed for ordinary directly buried and pipeline optical cables, and steel wire armoring must be used for submarine optical cables.
(2) Steel Tape Armoring. Most of the steel belts for armour are phosphorus-plated steel strips, and there are also galvanized steel strips. The number, thickness and width of steel strip are selected according to the diameter of optical cable before armoring.
5 Integrated Jacketing Production Line. 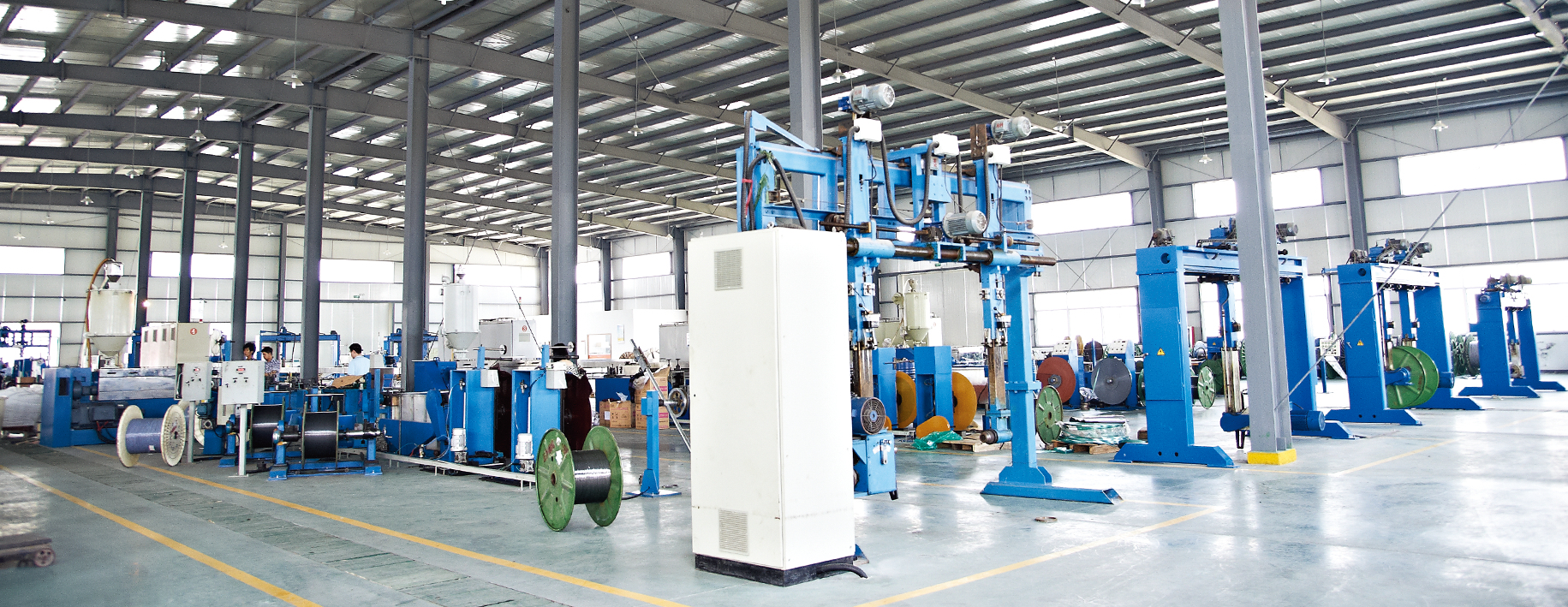
The integrated Jacketing production line and equipment is the special production line equipment for the last processing process in the manufacturing process of optical cable. This process can be subdivided into the following steps.
Cable core release, Cable core water resistance treatment,Aluminum-plastic belt / steel-plastic belt longitudinal Jacketing (or extruded plastic sheath), armoring, Plastic extrusion,Cooling, Printing, Spark monitoring,Take-up cable.